You can achieve a beautiful and aesthetically pleasing look for a building by using a rich variety of materials and types of facade siding. Siding is the cladding of a building's walls with finishing materials of different textures, shapes, sizes, and color palettes.
Among the vast selection of materials, we recommend using fiber cement siding, which is developed using the latest technologies in modern finishing. Fiber cement is simultaneously the strongest and lightest material, boasting excellent durability and serving you for many years without replacement. It's a trend of the past decade that will remain relevant for a long time to come.

The façade is clad with metal cassettes and fiber cement (our work)
Front siding comes in the form of single strips or ready-made panels. Panels are more popular, significantly simplifying installation work and reducing the time required for completion.
On one side of the panel (or strip), there is a fastening base with perforations, allowing the siding to be secured with screws to the sheathing. This makes them easy to install and easy to remove in case of damage or replacement.
Siding serves the following important functions:
Utilitarian - it protects the building's walls from external natural factors, mechanical damage, and chemical exposure.
Aesthetic - it decorates the facade and gives the building a beautiful and presentable appearance.
The size range of siding varies considerably because there is a wide variety of materials for facade finishing these days. Therefore, the size of a specific facade panel will depend on the chosen material and its manufacturer.
Siding comes in several varieties depending on the material it is made from, including metal, wood-plastic composite (WPC), fiber cement, vinyl, acrylic, polymer, HPL facades, sandwich panels, and reinforced foam plastic. More details about these are explained below.
1. Metal siding

Combined façade made of metal siding and ceramic granite.
Metal siding is one of the most reliable finishing materials. It is produced from steel sheets coated with a polymer layer (made of polyurethane, plastisol, polyester) to protect the metal from corrosion.
The shapes, colors, and textures available in the construction market today are so diverse that they allow metal siding to imitate any other material.
There are several types of metal siding: ship lap (or board), metal soffit, wall, and woodgrain.
Panel dimensions: width 200-400 mm, length 0.5-6 m, thickness 0.45-0.6 mm.
Advantages of the material:
Resistance to rapid temperature fluctuations, frost resistance.
Long service life (up to 50 years).
Fire resistance.
Resistance to environmental factors.
Maintains its shape when heated.
Colorfastness. Does not fade.
Disadvantages of the material:
Possible deformation upon localized mechanical impact.
Poor sound insulation.
In case of material ignition beneath the panels, it is difficult to reach the fire source because the metal becomes hot.
2. DPC siding.
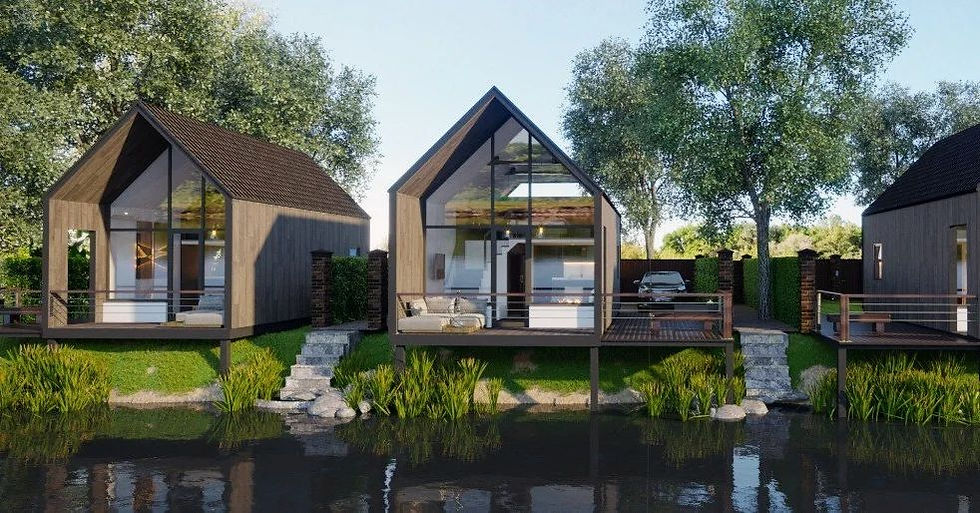
Facing the facade with DPC siding (our work)
Some consumers in their vocabulary use the phrase "wooden siding," which, essentially, is not entirely correct unless you mean cladding the facade with natural wood.
Technically, it is correct to say "wood-polymer composite (WPC) siding." The process of manufacturing such panels involves mixing wood and monomers that undergo polymerization. Chopped wood and polypropylene or polyvinyl chloride, as well as various modifying additives, are used in the process. The optimal ratio of components is 50% wood and 50% polymer. The required shape is achieved through extrusion. Externally, the texture of the panels mimics natural wood.
The installation of the panels is carried out on a wooden or steel frame. An important point is the presence of a gap between the cladding material and the main wall, which is necessary for the free circulation of air masses.
The average size of the material is: width 140-205 mm, thickness 13.5-16 mm, length 3-6 m.
Advantages of the material:
Durability, mechanical strength, preventing damage from impacts, scratches, and chips.
Resistance to temperature fluctuations.
Resistance to moisture, weak acidic and alkaline solutions.
Elimination of the risk of cracking and deformation.
Presence of a polymer film providing protection against mold and rot.
Sound and thermal insulation for the house. Composite siding effectively reduces external noise and prevents heat loss, improving energy efficiency.
Ease of installation and replacement/dismantling work.
Disadvantages of the material:
High cost.
Fading. Budget models of WPC can fade within a few seasons.
Thermal expansion. It is typical for many types of cladding products. To compensate for it, gaps of up to 5 mm are created.
3. Фиброцементный сайдинг (стеклофибробетон)

Fibercement siding for finishing
Fiber cement siding is an innovative composite finishing material. In Latin, "fibro" means "fiber," and "caementum" means "cement" or "quarried stone." These panels are made from high-quality cement mixed with quartz and other fillers, with fiber reinforcement added. Mineral additives include quartz crumbs, mica, and marble. Each manufacturer has its own composition for fiber cement siding and its own method of producing the material, which goes by several names (but each is correct):
Fiber cement
Glass fiber cement (glass fiber-reinforced concrete)
Glass cement
Siding dimensions vary: thickness ranges from 8 to 35 mm, width from 200 to 910 mm, and length from 1820 to 3030 mm. The material is available in the form of long boards of various thicknesses and widths, as well as in the form of sheets of different formats.
Advantages of the material:
High operational qualities. Strength and durability.
Excellent protective functions.
Resistance to temperature fluctuations and ultraviolet radiation.
Non-corrosive, non-decaying, and non-drying.
Absolute fire safety. The material is non-flammable, non-smoldering, and does not melt when exposed to direct flames.
Good thermal insulation.
Comparatively low weight.
Environmentally friendly.
Disadvantages of the material:
Vulnerability to prolonged exposure to moisture.
Specific installation requirements.
Relatively high cost due to the novelty of the material on the market.
4. Vinyl siding (polymeric siding)

The house is clad with vinyl siding
Vinyl siding in the form of panels is manufactured using polyvinyl chloride (PVC), various modifiers, colorants, pigments, and other chemical additives. A specific panel profile is achieved through the extrusion method - the alloy is pushed through an opening with a predetermined shape and then cut to the desired size.
Thanks to this composition, vinyl panels are quite rigid and durable, providing protection to the walls of the house against external factors and weather conditions, which is due to the presence of titanium dioxide. This material is incredibly popular, cost-effective, easy to install, and resistant to moisture and fire.
Panel dimensions: thickness 1.1-1.5 mm, width 205-255 mm, length 3-3.85 m.
Advantages of the material:
Long service life.
Does not absorb moisture, does not rot, and does not require additional treatment with special pest control agents.
Easy installation.
Resistance to rapid temperature changes.
Resistant to sunlight, does not fade.
Low specific weight.
Low maintenance.
Disadvantages of the material:
Low impact resistance at low temperatures (below -35°C).
Requires additional insulation for thermal insulation of the facade. Using only vinyl siding will not be sufficient.
Not entirely fireproof. Has a fire rating of G2.
5. Acrylic siding

Acrylic siding in the facade finishing of the house
Acrylic siding is produced using the same technology as vinyl siding, so externally, the panels closely resemble each other, and they are often confused. Overall, acrylic siding retains all the advantages of vinyl siding and surpasses it in some parameters.
The key difference lies in the preparation of the raw materials and the careful selection of components. Acrylic panels are primarily made from acrylic polymers, to which special polymer additives ASA (Acrylnitril-Styrol-Acrylester) are added. Additionally, acrylic siding incorporates: biochemical stabilizers, antistatic agents, flame retardants, and special reagents.
Acrylic siding is considered more resistant to ultraviolet radiation, mechanical damage, and thermal effects. Compared to vinyl, acrylic panels cost nearly twice as much.
Panel dimensions: thickness 1.1-1.5 mm, width 205-255 mm, length 3-3.85 m.
Advantages of the material:
High strength against mechanical and climatic loads, heat, chemical compositions, and aggressive environmental factors.
Resistance to rapid temperature fluctuations and frost.
No shrinkage after installation, maintains its shape and color throughout its service life. Does not fade in the sun.
Low specific weight.
Easy to install.
Disadvantages of the material:
There is a risk of mold development in humid climates.
Higher cost compared to other available types of siding (metal, vinyl).
6. HPL facade

The building facade is covered with HPL panels
HPL panels are a modern innovative material for both interior and exterior building cladding. They take the form of large-format decorative sheets with precise geometric shapes and can also have custom smooth contours.
The abbreviation HPL stands for High Pressure Laminate, which translates to "high-pressure laminate." However, it should not be confused with the conventional laminate we are familiar with.
HPL panels are based on cellulose impregnated with thermosetting resins, combined with several layers of decorative paper, and then subjected to pressure of 5-10 MPa. In the final stage, the panels are coated with high-quality acrylic, protecting them from all weather conditions. The result is a material with unique properties.
The dimensions of these panels vary within the following ranges: width 1.3 - 1.85 m, length 1.1 - 4.1 m, thickness 0.6 - 26 mm. Nowadays, it is possible to manufacture panels in custom sizes.
In the market of finishing materials, HPL panels are available in a wide range of colors, shades, and various textures, including wood, metal, and stone.
Advantages of the material:
High strength: The panels are resistant to scratches and other forms of damage.
Lightweight, placing a minimal load on the foundation.
Resistance to moisture, sunlight, and temperature fluctuations.
Low maintenance requirements: Easy to clean, resistant to microbial growth, dust and paint do not absorb.
Easy installation.
Wide variety of colors and textures.
Disadvantages of the material:
Flammability: It can withstand brief exposure to temperatures up to +180°C, but it can ignite afterward. According to fire safety standards, this material cannot be used in elevators, vestibules, or stairwells.
Poor resistance to wind loads due to the large panel area, especially when installation techniques are not followed correctly; panels may detach from the facade.
High cost.
7. Sandwich panels

Solar panel system
Sandwich panels are a modular system consisting of several layers: two external rigid layers and a layer of thermal insulation material (foamed or extruded polymer or mineral wool) located between them. The thermal insulation layer is enclosed on both sides by protective PVC sheets (or MDF, OSB, metal (steel or aluminum sheet), hardboard, plastic, or magnesite). The front side typically features a higher quality glossy or matte plastic, while the interior side has a durable rough sheet to which adhesive is applied.
Sandwich panels are used both in finishing the facades of buildings and in the construction, reconstruction, or insulation of old houses with weak structural elements. Depending on the type of internal thermal insulation, panels can be categorized as follows:
Polystyrene Panels: Used in the construction of industrial buildings and for various refrigeration installations.
Polyurethane Panels: Known for their excellent insulating properties, they are often installed on walls or roofs in the construction of factory facilities or warehouses.
Mineral Wool Panels: These panels have excellent fire-resistant properties and are primarily used in the construction of houses and food industry facilities.
The average size of a sandwich panel sheet is a width (height) of 1000-1200 mm, a thickness of 5-25 mm, and a length that can reach 8-13.5 m.
Advantages of the Material:
Affordable price.
Lightweight.
Excellent insulation properties.
Good resistance to moisture, fire, and decay.
Strength: Buildings constructed using sandwich panels are as strong as those made of concrete and blocks.
Low maintenance.
Rapid construction technology.
Disadvantages of the Material:
Non-load-bearing wall structure; additional loads are not allowed.
Fragility of external layers.
Strict adherence to installation recommendations is required.
8. Reinforced foam plastic
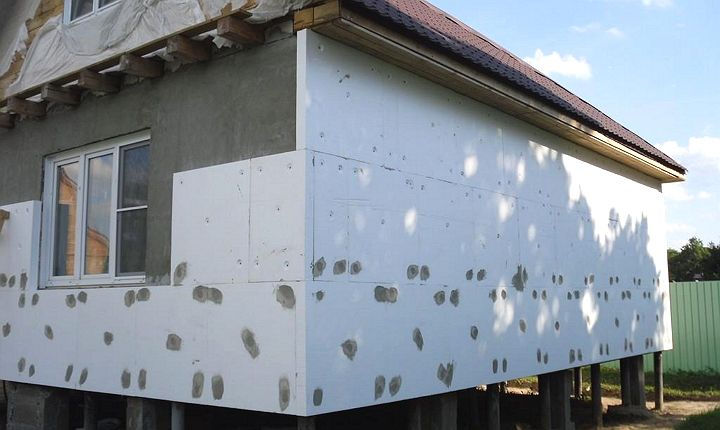
Installation of reinforced foam insulation
Reinforced foam insulation (also known as "isociding") is a sheet of dense expanded polystyrene reinforced with a mesh. A layer of special elastic plaster is applied to the front surface of the expanded polystyrene. This coating effectively protects the foam insulation from various atmospheric and mechanical influences. A decorative layer of facade finishing material, such as brick panels, can be added on top.
Facade reinforced foam insulation combines high thermal insulation properties and prevents the formation of cracks on the facade. This material is typically used in the renovation of old buildings. Manufacturers offer standard sizes of foam insulation sheets: width of 0.5-1 meter, length of 1-2 meters, thickness of 10-500 millimeters. This material can be easily cut to the desired size.
Advantages of the material:
Affordable price.
Lightweight.
Minimal load on the structure of the building.
High adhesion to any base material.
Does not create condensation on internal surfaces due to the presence of small vertical channels.
High resistance to temperature fluctuations and exposure to atmospheric precipitation.
Ease of installation.
Disadvantages of the material:
Not resistant to technical fluids.
Potential for mold or mildew growth.
High fire hazard, quick ignition in case of a fire.
Comments